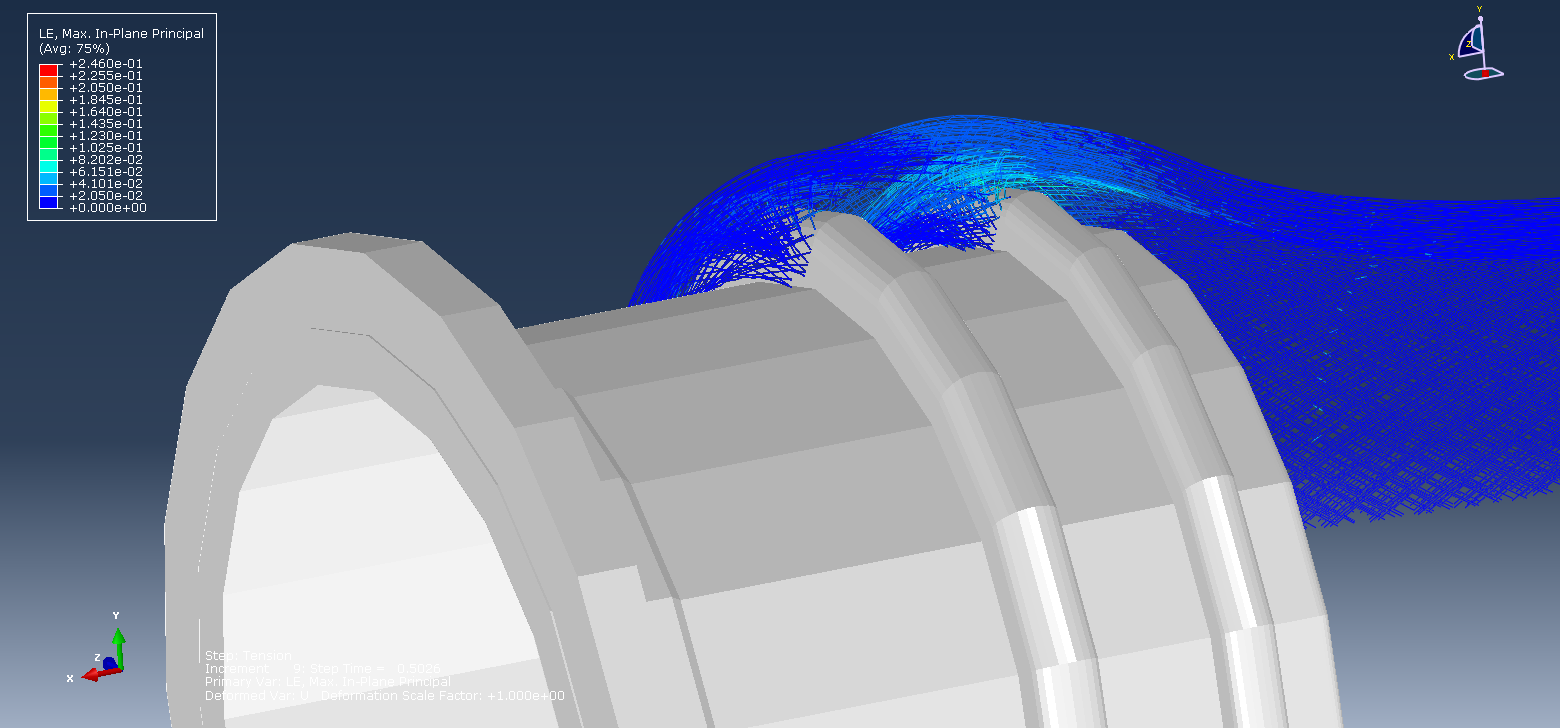
Design & Analysis Software
Software for design and analysis of reinforced rubber products
TANIQ uses advanced mathematical models and algorithms for designing optimal shapes and cord reinforcement structures, calculating burst pressures and predicting product behaviour for various load cases. To be able to use all this technology and know-how in the design process TANIQ has developed their own Design Software called TANIQ WIND®. This Composite Design Software is used for internal R&D projects and customer development projects. In addition, TANIQ has developed an FEA Toolbox for analysis of reinforced rubber products. The FEA Toolbox can be used to analyze the product behavior for different load cases, or to compare different designs. Analyzing and optimizing the design in a digital environment, can significantly reduce the required time and costs for prototype development and testing. TANIQ has developed a unique software platform and continuously refines and extends the functionalities of the Design and FEA Software.
TANIQ WIND® Software Platform
TANIQ’s software developers continuously work on optimizing existing code or developing new algorithms required for new designs or winding processes. After validation of newly developed code, it will be added to TANIQ WIND® for general use by all TANIQ Engineers. TANIQ WIND® provides extensive design options and material libraries for making reinforced rubber products, and creating production programs for various robotic set-ups.
For a number of focus applications TANIQ has invested in the development of design wizards, having customized user interfaces to guide the user through the design process, while providing design feedback and restricting the design space within predetermined (proven) boundaries. Such wizards enable unexperienced users to make high quality product designs after only 2 days of training. This enables TANIQ to develop these Applications faster and more efficiently. Furthermore, these wizards form the basis for the custom developed Design Software for TANIQ’s customers.
Current wizards:
Expansion Joint Software
Pipe Plug Software
Large Hose Software
Because the customer software is based on the TANIQ WIND® Software platform, all benefit from updates, improvements and new features. Innovation and consistent development (of the platform) are key within TANIQ.
Finite Element Analysis for reinforced rubber products
TANIQ has developed their own Finite Element Analysis model to further optimize the product design process. TANIQ has developed accurate material models for commonly used reinforcement cords and rubbers, and modelled the interactions between rubber and cord elements, and metal couplings/flanges. The FEA model has been validated by extensive product tests results of pipe-plugs and expansion joints which showed very reliable results. Exactly knowing the positions of the reinforcement cords enables TANIQ to make very accurate FEA models which represent the actual product very realistically.
As part of optimizing reinforcement structures TANIQ computes the optimal position of the reinforcement cords (e.g. geodesic winding paths) and accurately places the cords on their predetermined positions using industrial robotics. Furthermore, an entire reinforcement layer is build using continuous cords (e.g. 4 cords), which run back-and-forth over the product, typically integrally overwinding product flanges or couplings as well in one go. As a result the materials will be accurately positioned according to the predetermined positions in the design made with the software. Therefore, TANIQ’s Technology provides a unique consistency between the product design made with the software, the design analyzed with the FEA Software, and the actual product build with the robot.
The FEA is currently used for optimizing designs in internal R&D projects and for product development projects for customers. To create a user-friendly coupling between the Design Software and FEA software, a FEA Toolbox was developed. A design made with the Design Software can be directly imported in the FEA Toolbox, where various load cases can be generated. Next, an import file is created which can be automatically run in commercial FEA packages such as Abaqus. As an additional feature customized FEA reports can be generated.
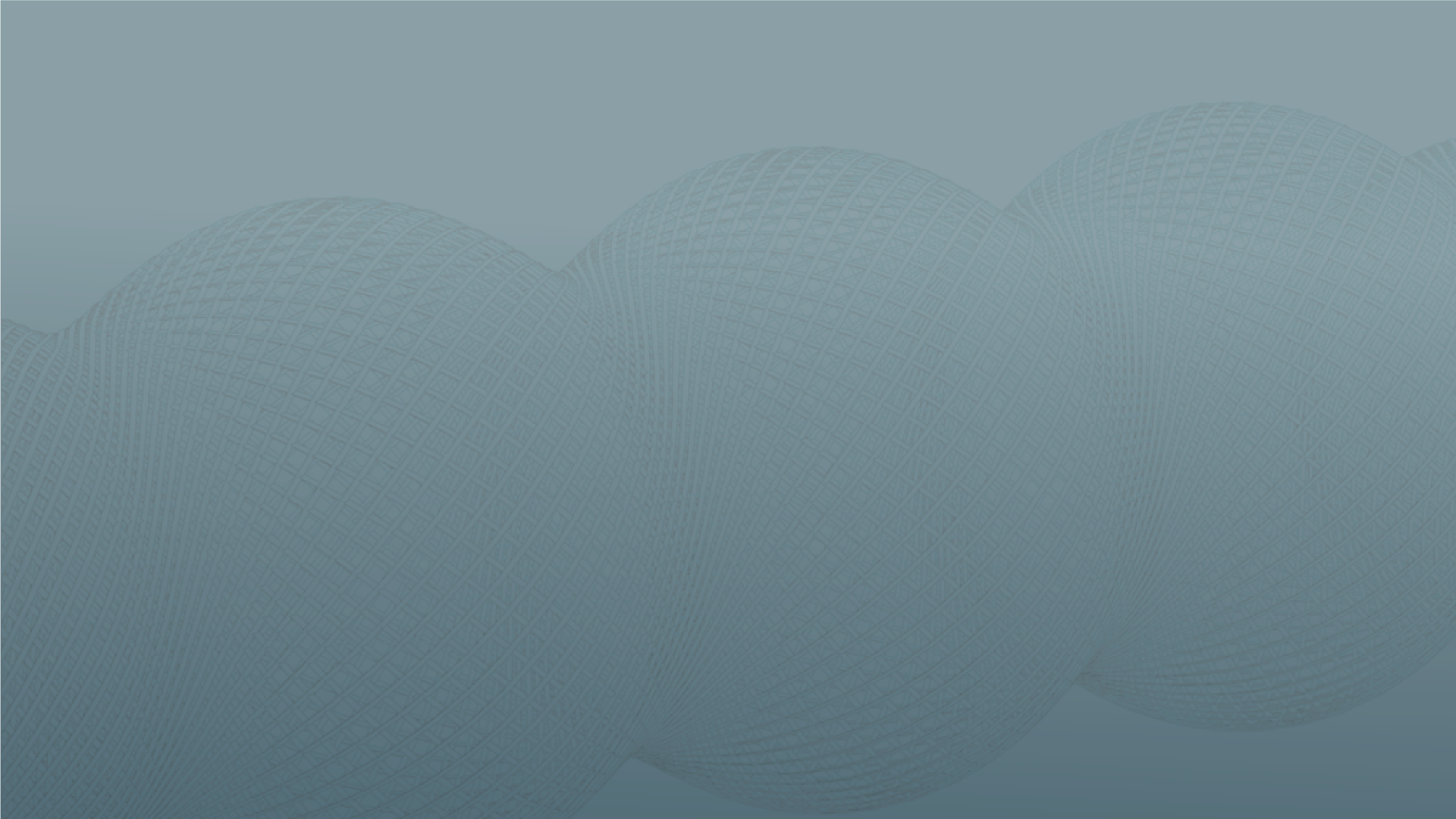