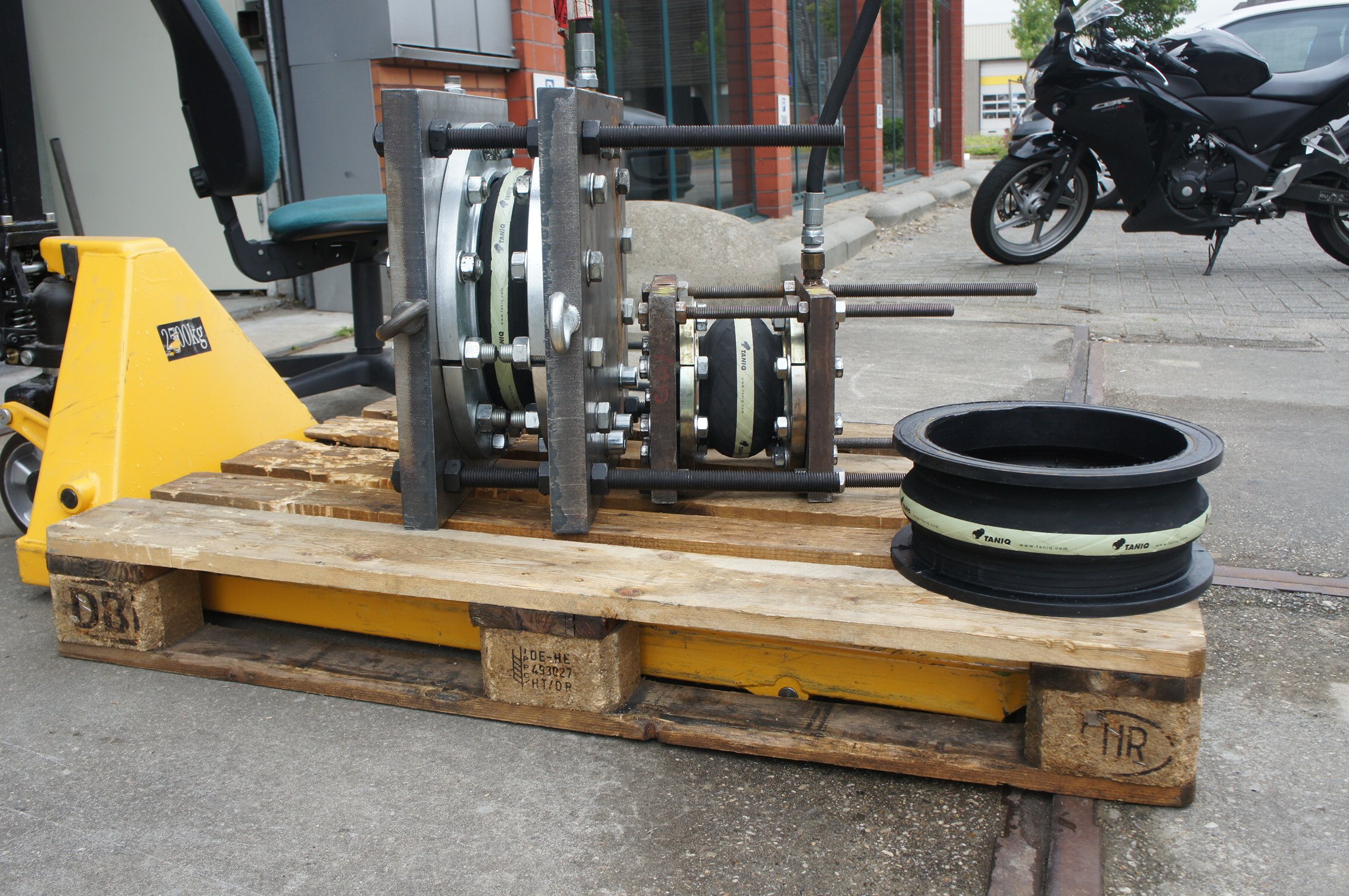
Rubber Expansion Joints
Smart Factory for Rubber Expansion Joints
Rubber expansion joints are engineered rubber products that are inserted in rigid piping systems to absorb movements, improve thermal stability and compensate for misalignment. Their performance is crucial for the safety and reliability of the entire system.
TANIQ has developed an optimized method for designing and manufacturing rubber expansion joints resulting in a higher performance and reliability. The optimized design methodology follows lightweight engineering principles , whereby the design is optimized using mathematical and finite element models. Using in-house developed winding equipment all materials are then accurately placed during production. This digitized design and automated manufacturing process introduces various advantages in terms of costs savings, improved quality and consistency.
To make the technology and knowledge easily accessible to their Clients TANIQ has developed user-friendly software for making designs and machine code. With this software the product can be designed, analyzed and optimized in a digital models before physical production. Furthermore, the software simulates the entire production on a digital twin to check for possible collisions and to optimize the machine paths for speed and accuracy, and to predict production times. Having the design and production program simulated and optimized in a digital environment enables first-time-right production.
Rubber Expansion Joints
State-of-the-art
For optimizing the rubber expansion joint design, first the current design and production process were analyzed. All high-end rubber expansion joints are mandrel-built, whereby the material layers are manually applied by a skilled worker. The reinforcement cords are embedded/skimmed with rubber and applied in sheet form. Typically, the reinforcement is applied in pairs of two, having the cord angles in opposite directions. At the ends the materials are cut and folded under/over the flanges.
The main limitation for further optimization of a rubber expansion joint using this method is i) the use of the skimmed cords and ii) the manual application thereof. The width of the sheet makes it impossible to have the individual cords positioned most efficiently. The manual application makes it even more difficult to place the materials on their optimal positions and do this consistently for each piece of material in the product. Working in pairs of two, will always require an addition of two extra layers, also when only little extra material would be needed to reach the desired working pressure.
Optimized rubber expansion joint design
The optimized rubber expansion joint design is like generally known designs, having an inner rubber liner, rubberized reinforcement layers and outer rubber layer. A distinct difference is however that the reinforcement layers are constructed of individual cords which are integrally wound on the product body and flanges in a continuous fashion. This has the following advantages:
Minimum amount of reinforcement cords > less material, lighter, more flexible;
Accurate positioning of all materials > consistent and reliable product;
Continuous and seamless reinforcement layer > no stress introduced by seams or overlapping plies ;
Interwoven layer (instead of paired layers) > prevents risk of layer delamination.
Following these design optimizations up to 50% of the reinforcement materials can be saved, resulting in costs savings and performance improvements.
Optimized rubber expansion joint design
Product analysis and simulation using finite element analysis
To analyze a product design and simulate its behavior under different loading conditions Finite Element analysis can be used. The quality of the FEA is determined by the quality of the model. TANIQ has developed their own FE modelling, including smart rubber-to-cord meshing strategies. The FE modelling has been validated by product testing for rubber expansion joints up to ID1200mm. Compared to manually manufactured rubber expansion joints, the automated manufactured expansion joints show unique consistency between the digital three-dimensional design, FE model and the actual product.
FEA has been successfully applied for optimizing rubber expansion joints for large movement compensations up to 80mm in lateral and axial directions. From the simulations optimal bellow shapes and required number of bellows have been derived.
Automated manufacturing of rubber expansion joints
The manual manufacturing of mandrel-built rubber expansion joints is labor and skill intensive. Therefore, TANIQ has developed processes and equipment to automate the production. Automation results in significant production time reduction (up to 70% in some cases) and introduces high product quality and consistency. The automated production system can be operated by a single operator. The required knowledge is captured in the system software such that the operator can be trained in one week how to operate the the system and execute the few remaining manual operations.
Production process simulation and optimization
Similar as how a rubber expansion joint design can be simulated and optimized in a digital FE environment, the production process can be simulated and optimized in a digital environment as well. After making an optimal product design with the Design Software, the machine code can be generated automatically. As part of the process it will check for possible collisions between equipment and product during the process. Next, the production files can be loaded on the specified production system.
In addition, TANIQ has developed software for further optimization of the machine paths. This can be used to optimize a production program for speed or accuracy. By using optimizing techniques like smart point filtering and path optimizations TANIQ was able to improve the machine speed by 60%.
Material supply system having less waste
The currently used steel mandrels, rubber bellows and flange rings remain the same using the new technology. However, the introduction of automated winding individual cords, rubber strips and wrapping tape also changes the material supply side of rubber expansion joint manufacturing.
In the current situation all materials are cut to size following a Bill-Of-Materials (BOM) for each specific product. This also means that the rubberized/skimmed reinforcement cord are cut to size, leaving waste. In the new situation the bobbins with reinforcement cords are placed in the system and only refilled when empty. The same applies for the rubber, which is prepared in strip form on bobbins, and stored next to the production system. Per product the assigned type of rubber (e.g. NR or EPDM) can be loaded to the system. After production it can be stored again until it will be used for the next product. With the materials loaded on spools, there is no pre-cut material preparations needed anymore, and no more losses from cutting of preparation materials or waste during production. Additionally, having individual spools with cord materials and rubber makes it easier to combine different materials.
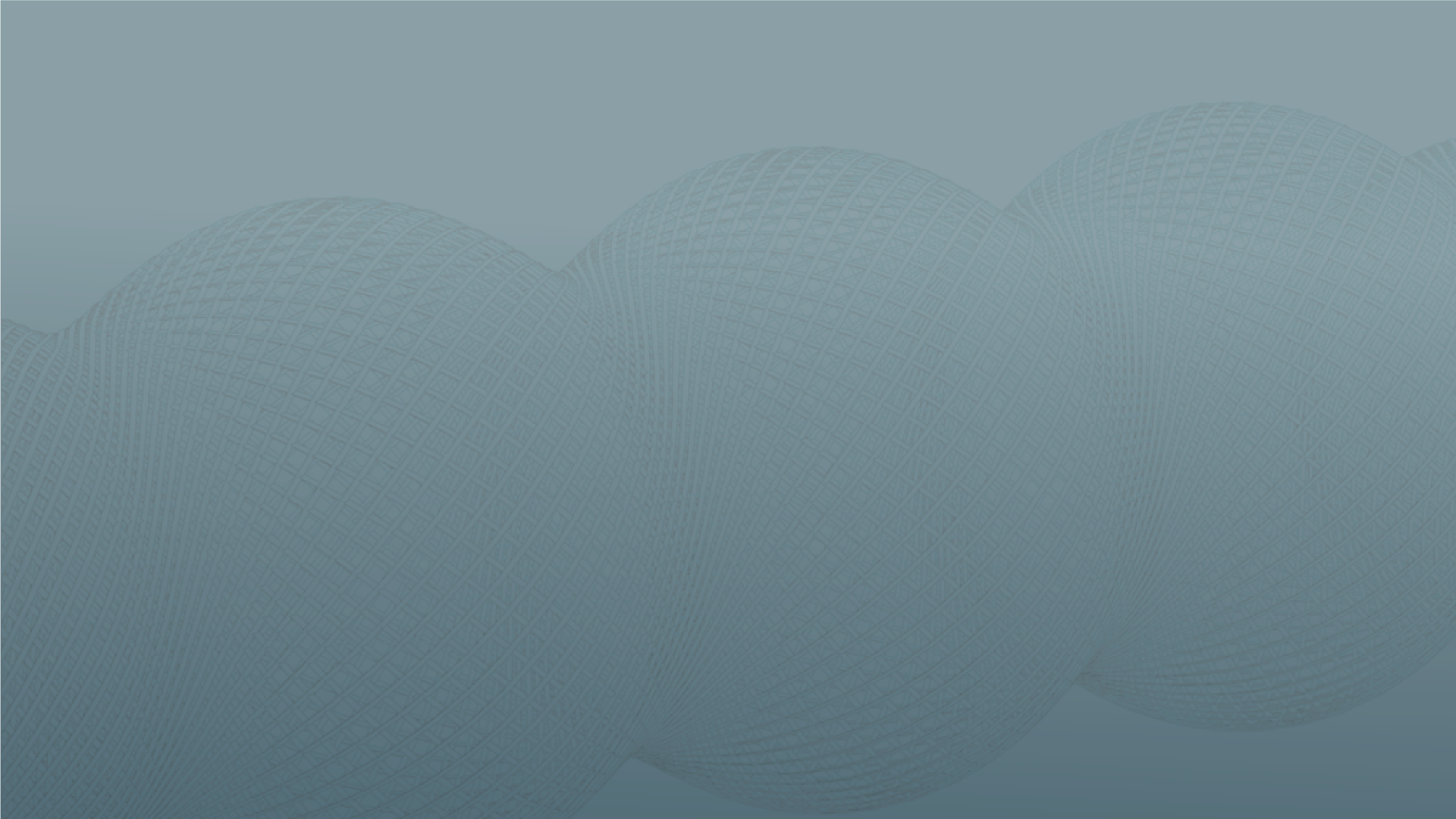