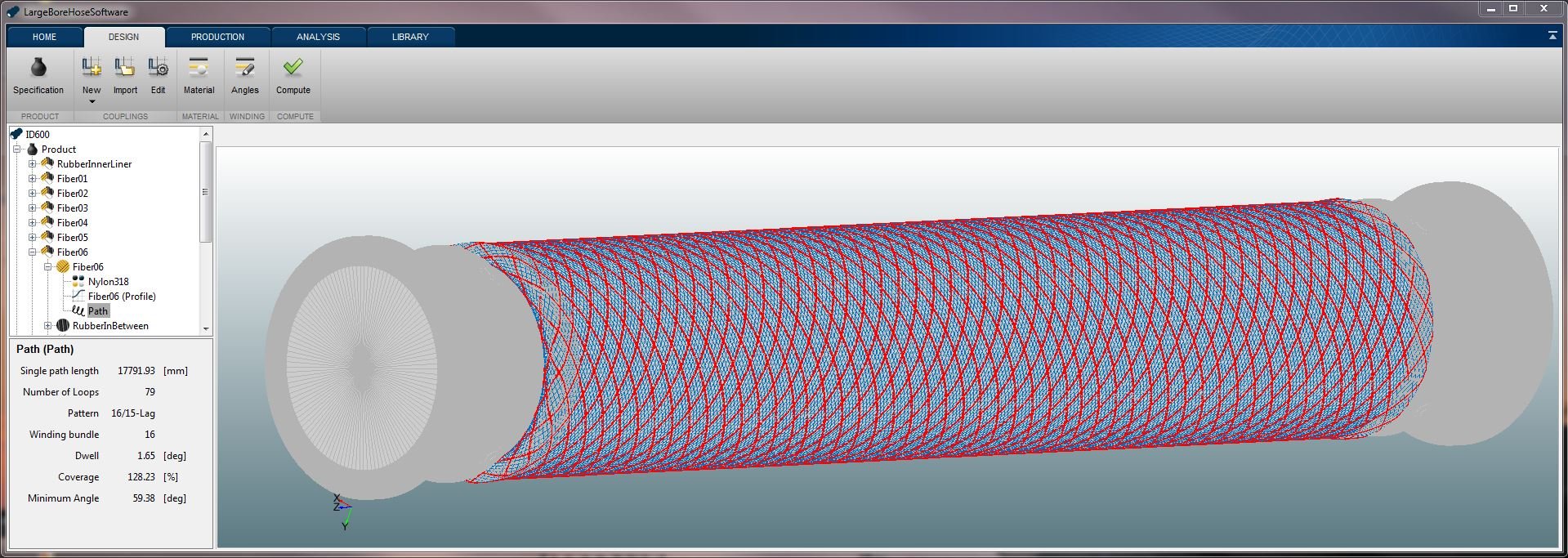
Rubber Design & Manufacturing Software
Software for design and manufacturing of reinforced rubber products
TANIQ develops powerful winding software for reinforced rubber products since 2006. TANIQ uses this fully in-house developed software for their R&D projects and for making custom Client software. In the past 17 years, TANIQ has developed a large variety of reinforced rubber products, developing unique expertise on design and automated winding of rubber products. Using this expertise TANIQ develops custom automation solutions for their Clients, enabling them to make new products fast and efficiently without significant training. This is achieved by embedding all required design and manufacturing knowledge in systems, a combination of CAD/CAM software and automated winding equipment.
Capturing the design and manufacturing knowledge in custom software ensures that the manufacturers are less dependent on their skilled personnel. With TANIQ’s custom software, an engineer can be trained in one week to design and manufacture advanced products such as rubber expansion joints, pipe plugs or mining hoses.
The key functionalities for CAD/CAM software are:
Designing of reinforced rubber products using a ‘Design Wizard’;
Generating winding programs (robotic and CNC);
Finite Element Analysis (FEA Toolbox for creating input models for Abaqus);
Simulating of winding processes in digital twin environment.
Designing rubber products made easy with a Design Wizard
An important part of the custom software is the Design Wizard, which guides the user through the design process for making their specific product requiring only parametric inputs. The advantage of using the Design Wizard is that the user, even without design or manufacturing experience, can design complicated products in only 15 minutes.
The design made with the software are directly uploaded to the winding equipment such that the products can be repeatedly made with the same high quality and consistency. Furthermore, the design can be imported in TANIQ’s FEA Toolbox for analysis of the design for different load cases in a digital environment. Optimizing designs using FEA saves significant time and money for physical prototyping and testing. Before running the actual production on the winding equipment, the production programs can be simulated on a digital twin to check for reachability and collisions, or for improving production times.
Conventional design and manufacturing of mandrel-built reinforced rubber and composite products requires skilled and experienced employees. It can take several months to years of training to become skilled in the art. Furthermore, making new designs strongly depends on their experience, and little on validated mathematical models. This results in dependency on skilled workers. The differences in skill/experience between workers will lead to variations in product quality. Furthermore, in case you want to upscale your production it will take time before new workers have sufficient skills and experience.
You can improve your situation by capturing your design and manufacturing know-how in the software program. Embedded mathematical models and design rules guarantee good product designs, independent of the designer. The design will be automatically manufactured, significantly reducing the chance of deviation in product quality or consistency.
Capture your know-how in software and become less dependent on skilled employees
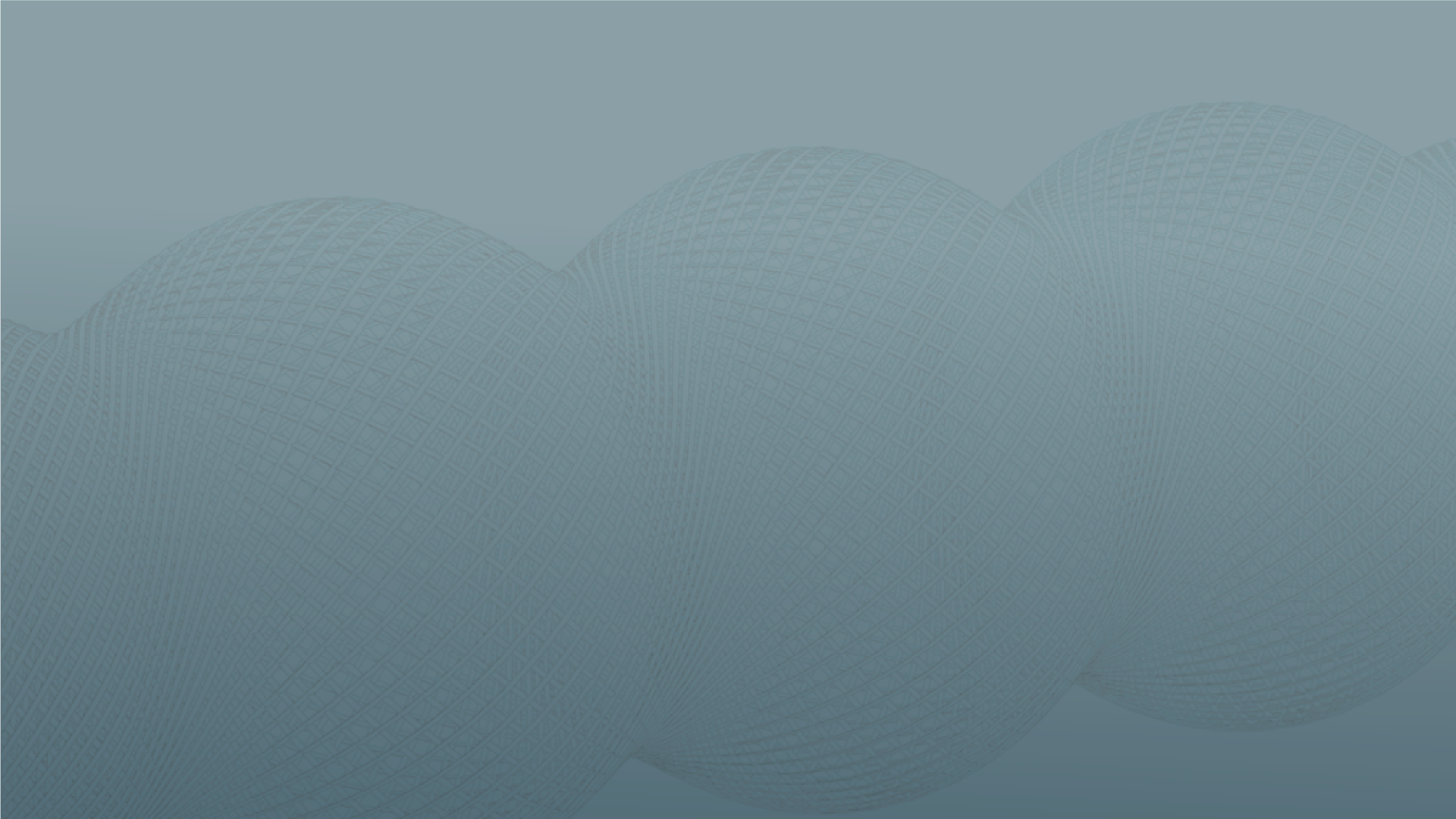