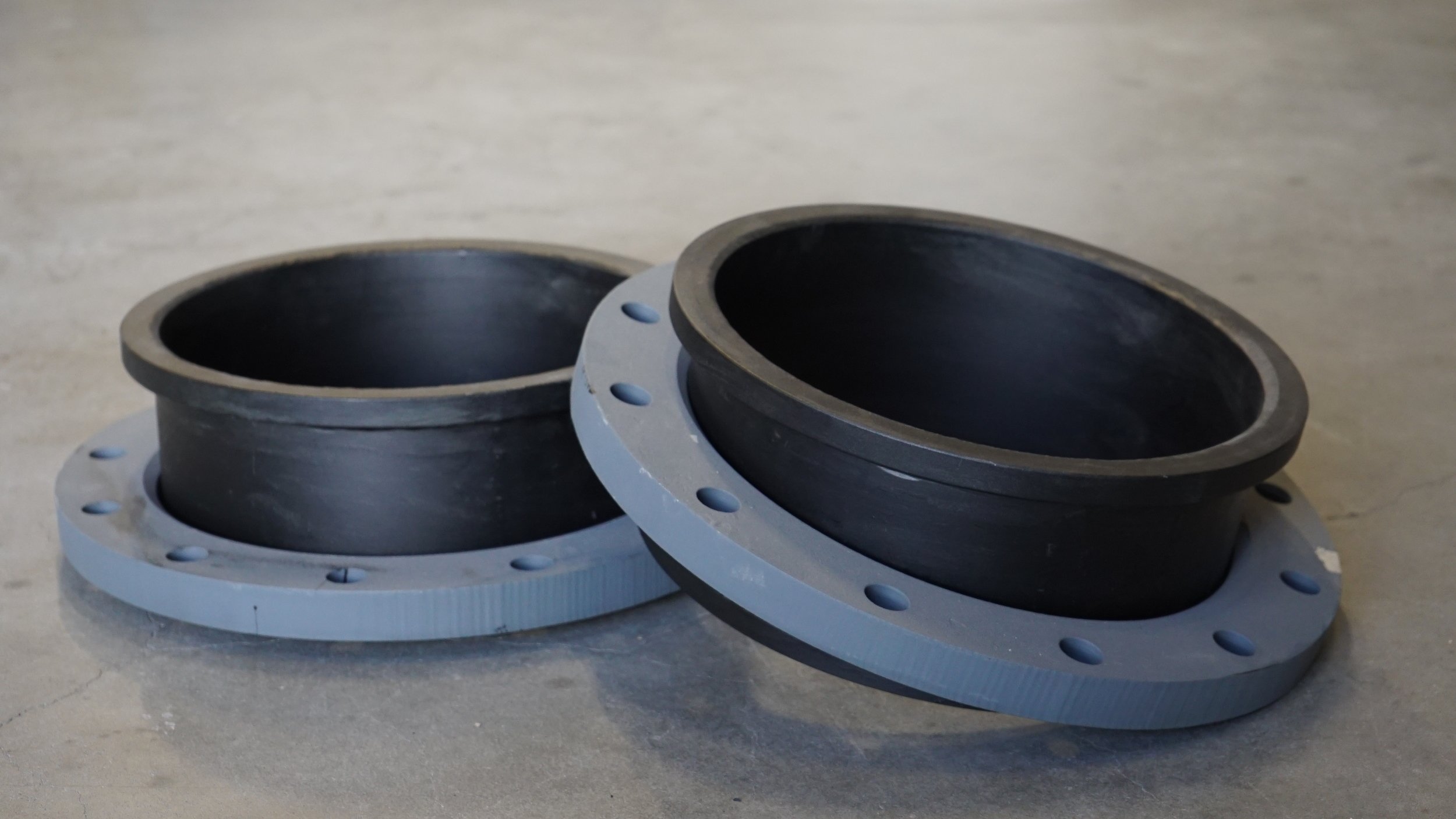
Couplings and Flanges
Design of (integrated) couplings and flanges for cord reinforced rubber products
TANIQ has developed new solutions to integrate flanges and couplings in your products more efficiently. The main principle is that the flanges and coupling are integrated in the product body by continuous winding with cords. Conventional processes mostly involve manual folding of fabric sheets to form the flange or coupling connection. Sometimes also metal wires are added to keep the folded structure in place. TANIQ's technology uses the tensile strength in the cords to make more efficient connections and even create self-sealing effects. The flanges and couplings have been successfully applied in pipe-plugs, air springs, large diameter hoses, pinch valve sleeves and lifting bags.
Integral reinforced flange
TANIQ has patented their technology on how to integrate flanges in cord reinforced products such as expansion joints, pinch valve sleeves and hoses with integrated rubber flanges. In the conventional designs these flanges are formed by folding of fabric sheet and rubber layers. TANIQ has developed a solution whereby these flanges are integrally overwound with the rest of the product body. The flange moulding process and the flange dimensions are the same as in the current production process. The advantage is that the entire process can be automated (no manual flange folding steps anymore) resulting in high consistency and significantly faster production.
Integral reinforced hose coupling
TANIQ is developing large diameter hoses for dredging and mining applications. These rubber hoses have integrated metal couplings with flanges. Typically these couplings comprise a metal cylindrical part with several retainer rings in circumferential direction. During production the fabric sheet materials is placed over these rings, metal wire is wound around the sheets pressing it against the metal coupling between the rings, after which the sheets are folded backwards again. TANIQ has developed a new technology whereby the reinforcement wires are wound behind the rings in a continuous winding process. No manual folding steps or winding of metal wires is needed anymore. The integral reinforced hose couplings have been successfully tested up to 90 bar burst pressure.
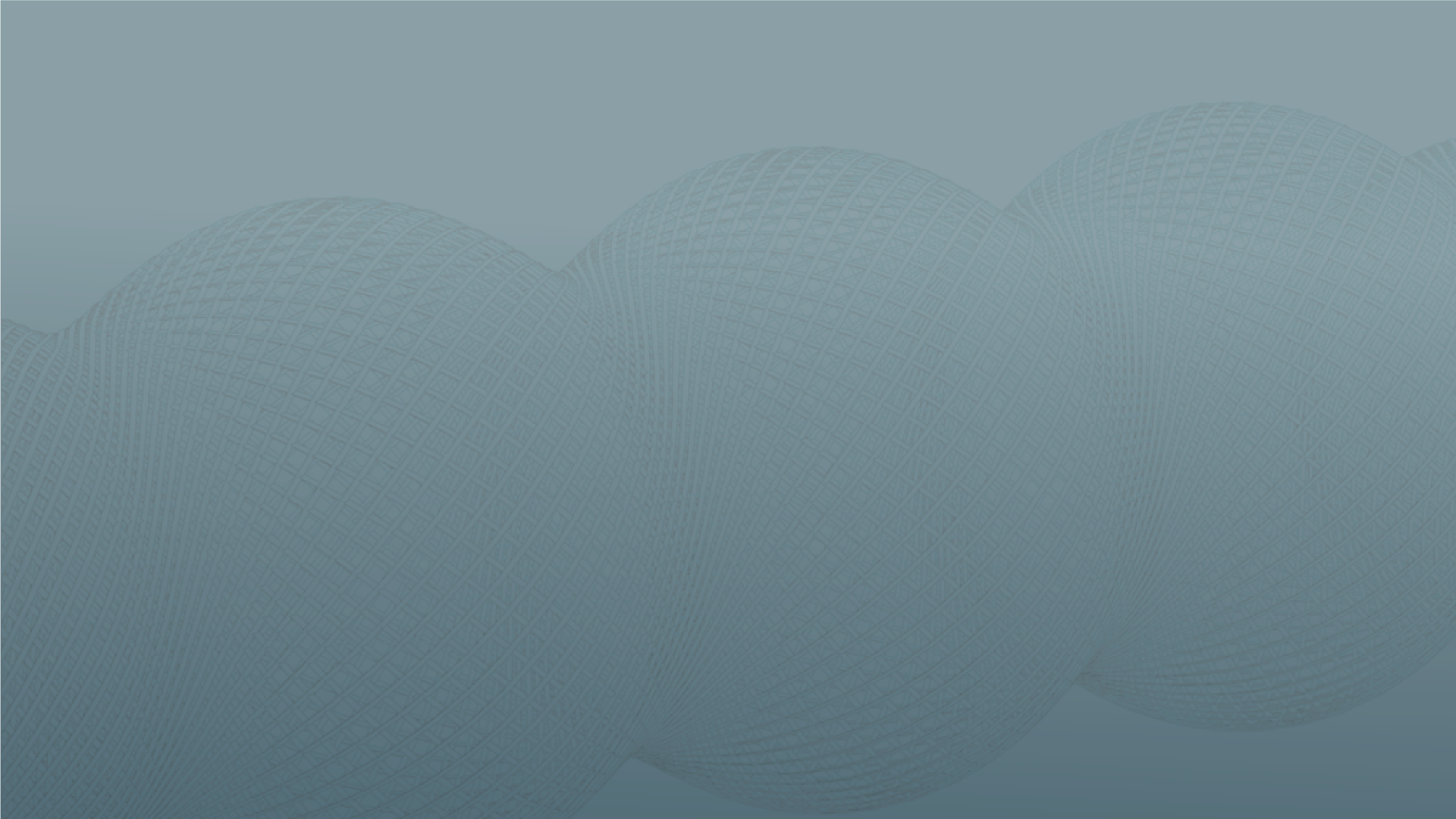