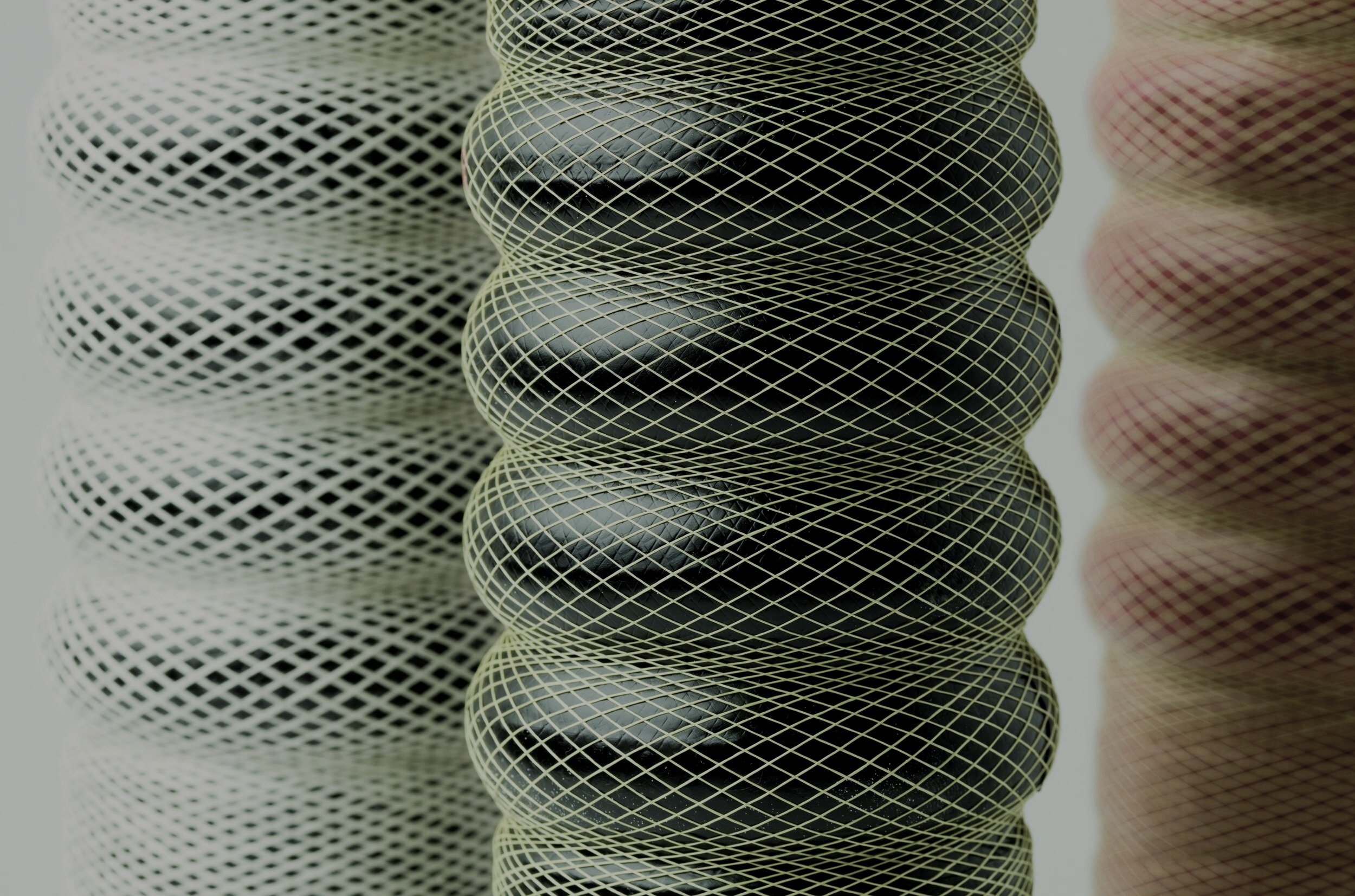
Convoluted Hoses
Turbo Hose / Charge air hose
TANIQ has invented a new technology for the reinforcement of turbo hoses for heavy duty vehicles. Instead of applying fabric reinforced rubber sheet material TANIQ has invented a new design for the reinforcement construction, so that the rubber and cord materials can be applied separately and used more efficiently. TANIQ has done intensive research and development on the design and automated production process of turbo hoses within TANIQ's EUREKA turbo hose project. TANIQ's technology works for both hot-side and cold-side hoses.
Optimised convoluted hoses with high pressure and temperature resistance
TANIQ's technology has shown to work well for both hot-side and cold-side hoses. For cold-side turbo hoses, automation of the production process using robotics results in faster production at lower costs. Automated production of hot-side turbo hoses is more challenging because of the properties of un-cured silicone rubber strips. The un-cured silicone's green strength can easily result in inconsistent strip dimensions during winding of the bellows at high production speeds. Therefore, errors can occur in the silicone rubber layer. TANIQ's material tensioning and application technology is continuously under development to eliminate these errors.
Convoluted hose reinforcement technology
The left image on the picture shows a conventional reinforcement structure of fabric reinforced rubber sheet. The right image shows a TANIQ reinforced rubber bellow using up to 50% less material as a result of optimised positioning of the cords and determining the optimal bellow shape.
The basic principle is to determine the optimal shape of the rubber bellows and calculate the accompanying cord paths over these bellows. Instead of wrapping rubber sheets with fabric reinforcement over these bellows, the rubber and cords are applied in separate steps. By applying the cords on the bellow shapes using accurate robotic equipment it becomes possible to place each individual cord on its optimal position. The isotensoid bellow shapes result in equal distribution of all forces along the convoluted turbo hose. By placing the cord on their optimal paths they are only loaded with tensile stress and all forces are fully adapted by the cords.
Automated (robotic) production of turbo hoses
TANIQ has developed a new production solution which enables a fully automated production process. The process involves automated placement of the inner and outer rubber layer, and an automated placement of the reinforcement structure. Finally, also the wrapping of nylon tapes for vulcanization is automated (constant force and standardized winding pattern). Therefore, only a minimum of manual labour is required to build the turbo hose and a repeatable high product quality can be achieved.
Turbo hose blow molding process
Besides automated placements of all turbo hose layers using robotic equipment TANIQ is also developing a blow moulding process for turbo hoses. In this process TANIQ makes cylindrical parts which are blow moulded into the bellowed hose shape of the turbo hose. The advantages are a high speed production speeds and very good tolerances. This development was tested within TANIQ's EUREKA turbo hose project.
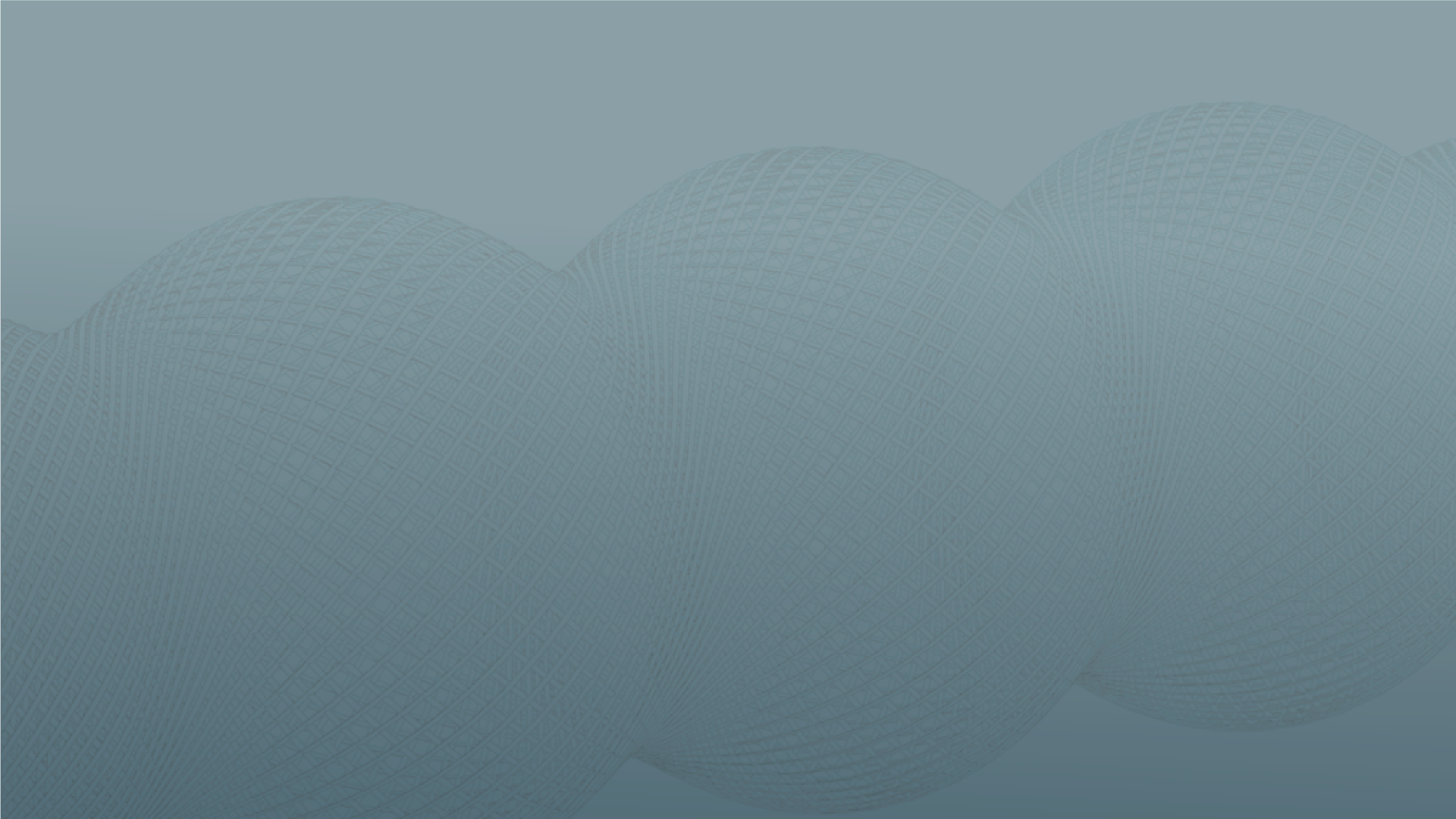