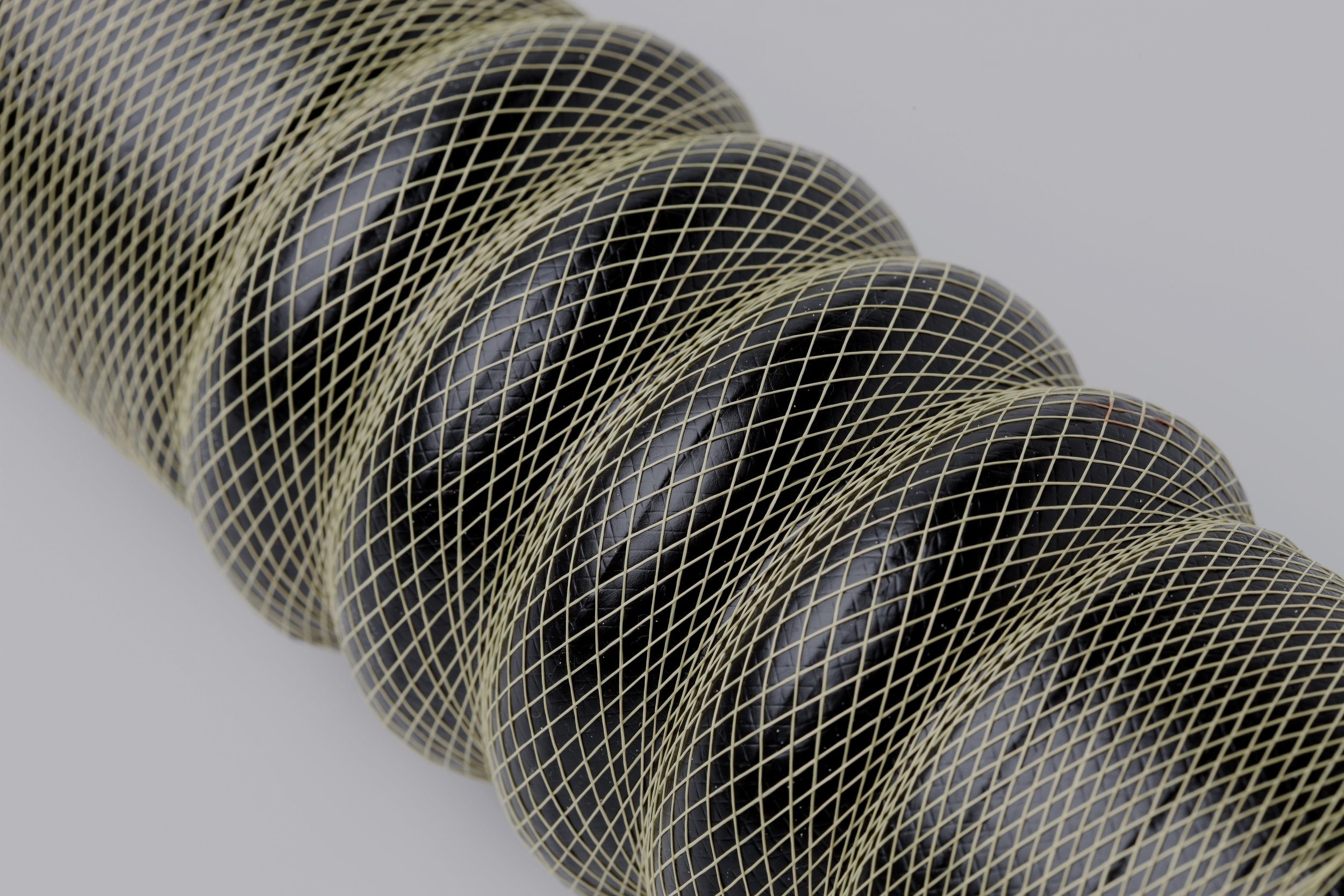
Optimised Cord Reinforcement
Research on cord reinforcement structures for rubber products
TANIQ is specialized in the design of cord reinforcement structures for rubber products. For optimal reinforcement of (rubber) products TANIQ uses design principles for lightweight engineering from the Aerospace industry (TANIQ is a spin-off from Aerospace Faculty of Delft Univeristy of Technology). TANIQ strives to optimize the use of the cords by calculating their optimal path trajectories (e.g. geodesic path) and accurately placing them on those trajectories using industrial robots.
Cord reinforced rubber products combine a rubber and a reinforcing material, so high strength to flexibility ratios can be achieved. The reinforcing material provides the strength and stiffness. Simultaniously, the rubber matrix, with low strength and stiffness, provides air-fluid sealing. By calculating the optimal product shape and by placing the cords on their ideal paths, the cords are purely loaded on tensile stress and use 100% of their strength. Under these conditions the cord structure takes up all the forces. Hence the rubber does not have to take up sheer stresses and is solely used for sealing. This way, both materials are used most efficiently. Furthermore, it also means that the reinforcement structure is in equilibrium state and therefore the product will not expand, shorten or lengthen under pressure. Knowing the force equilibrium of the reinforcement structure, it is also possible to deliberately adjust the product shape and path angles to obtain predictable and controlled shape expansion.
Geodesic cord paths and isotensoids
Two important design features are geodesic cord paths and isotensoid shapes. A geodesic path is the shorthest path between two points on a (curved) surface. In a reinforcement structure, placement on the geodesic path ensures efficient use and loading of the reinforcement material. A cord reinforced isotensoid shape is a shape where the resulting stresses are aligned with the cord direction resulting in constant stress throughout the product. As a result the cords in such product are purely loaded on tensile strength and the product will not deform under influence of internal pressure. Geodesic paths in combination with an isotensoid shape will result in optimised material usage and loading.
Neutral winding angle 54,7 degrees
The optimal path for reinforcement loading depends on the product's contours. In case of cylindrical products, the neutral winding angle (e.g. straight rubber hose) is approximately 54.7 degrees. Accurate placement of reinforcement cords on this path results in purely tensile stresses exerted on the reinforcement structure. Thereby, 100% of the load is absorbed by the cords for any pressure (up until the cords are loaded 100% of their tensile strength). Hence the rubber does not have to take up sheer stresses and is solely used for sealing. This way, both materials are used most efficiently. Furthermore, it also means that the reinforcement structure is in equilibrium state and therefore the product will not deform, expand, compress or elongate under pressure.
This basic principle for hoses also applies for convoluted products. However, calculation of this optimized angle is a lot more complex and depends on the local contour of each single point of the product. Hence, the angle at which optimized loading is realized varies over the product. TANIQ has developed algorithms to calculate the optimum path angles for any contour. These algorithms are incorporated in the design software to design the optimized reinforcement structure of any product.
Effects of cord reinforcement structures on dynamic behavior of bellow shaped hoses.
The use of individually winded cords in the reinforcement structure results in a high amount of cross point. Individual cords and cross points could have an effect on the dynamic behaviour of the product. Research on the effects on these cross points between cords has been executed. One specific research area has been to determine if a cross point free structure made with spiraling technology performs better on dynamic behavior. Other extensive tests have been performed to determine the dynamic behaviour and cord performance degredation at cross points due to friction.
Research on the dynamic behaviour of the cord structures and delopment of the structure design algorithms show consistent product behaviour and realisation of the designed product performance. Especilaly cross verification between the design software, FEA and actual products indicate high validaty. The hypothetical negative effect of cross points and cords on dynamic bahaviour has been eliminated.
Braided reinforcement structures for bellow shaped hoses - including prototyping at Euro Carbon
In addition to robotic winded cords, TANIQ has researched, developed and tested the feasibility of using braiding technology for the manufacturing of bellow-shaped hoses like charge air cooler hoses.
Optimization of reinforcement structure of reinforced elastomers hoses with additional plastic spiral (e.g. garden hose or petrol drop hose)
In addition to robotic winded cord structures, TANIQ has researched, developed and tested the use of additional reinforcement spirals for elastomer hoses and include the strength of the plastic spiral in the structure design algorithms. This technology is succesfuly applied in garden hoses.
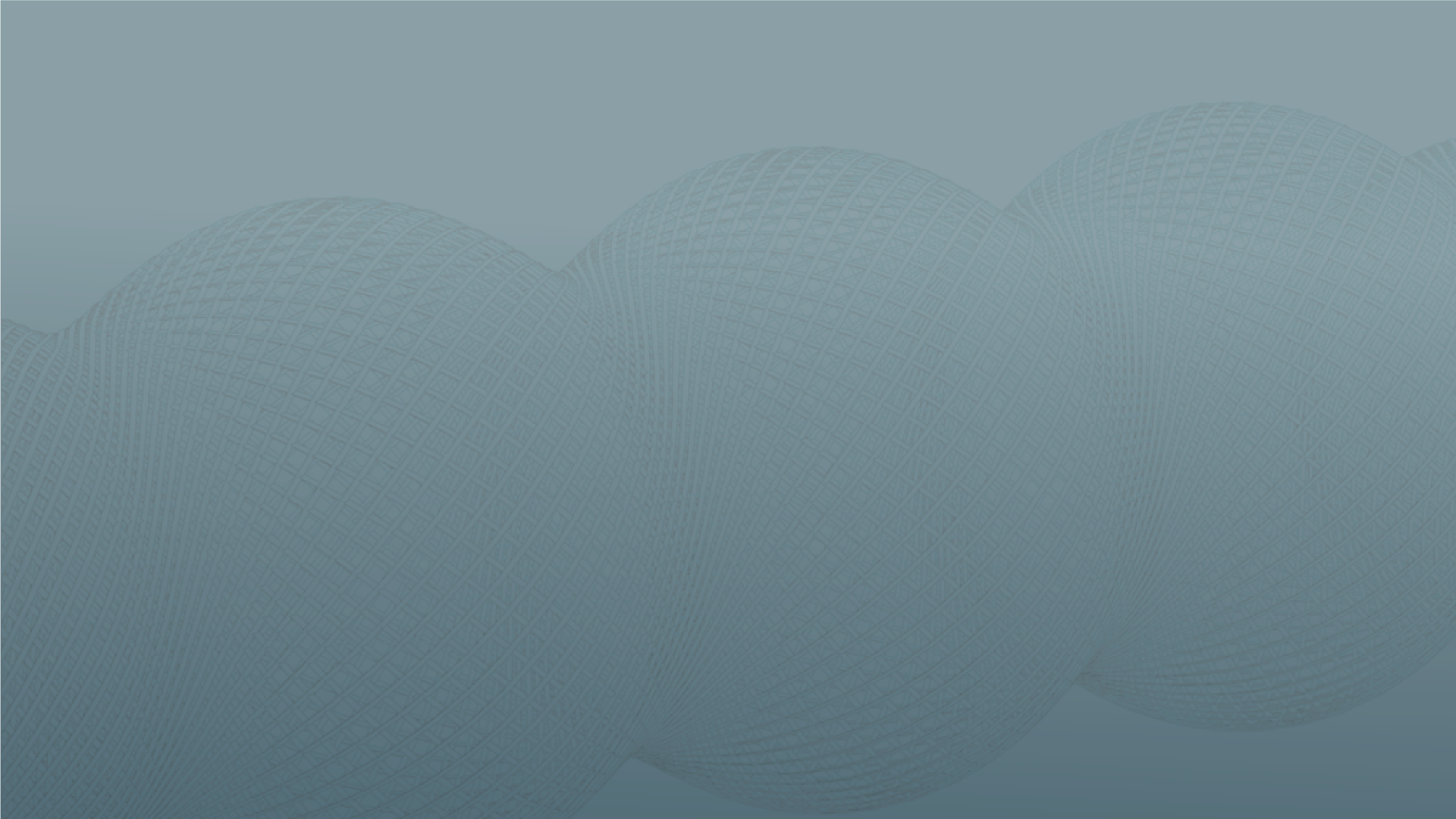