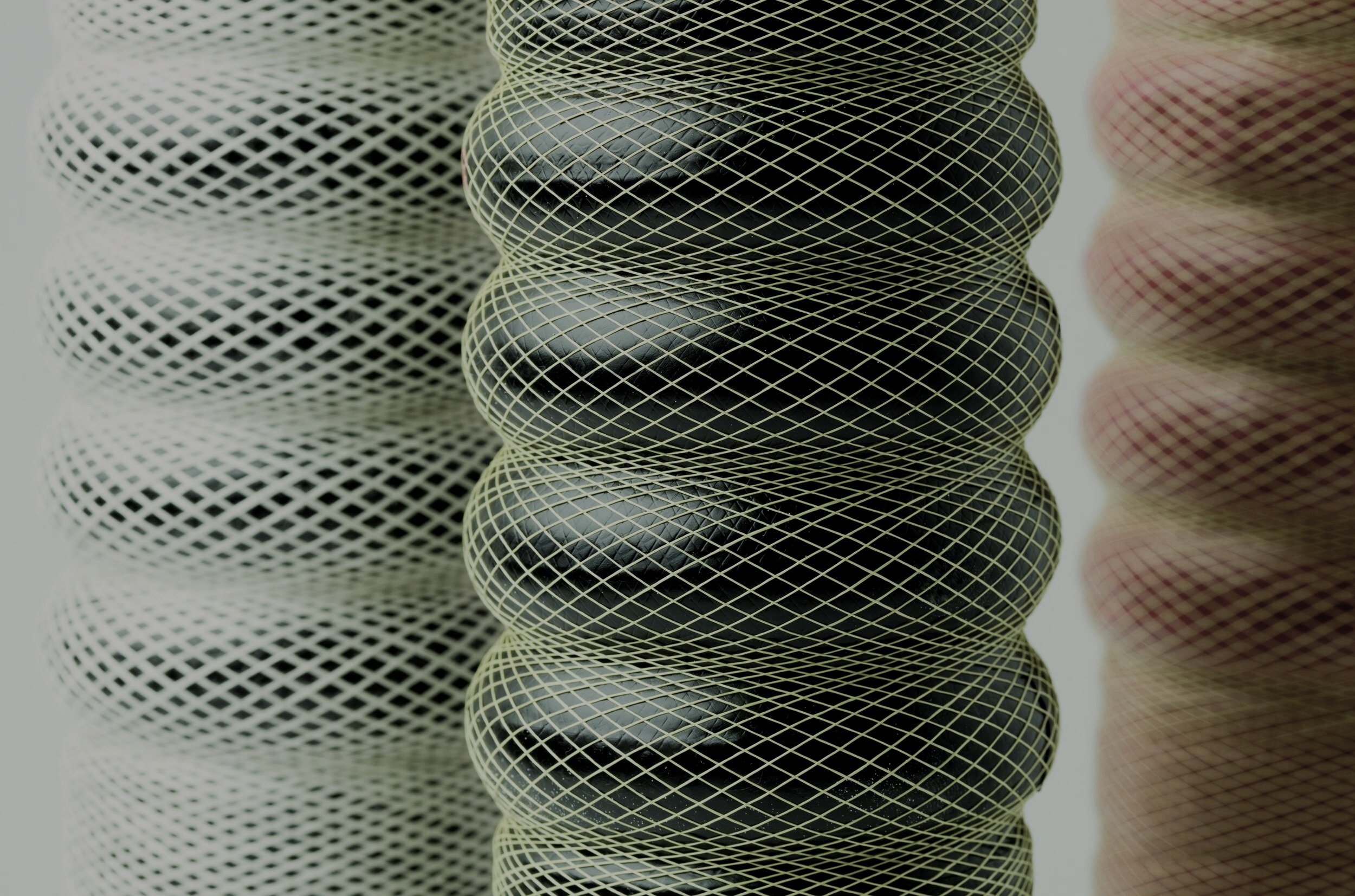
Multi-layer Reinforcement Optimisation
Multi-layer reinforcement structures for rubber products
TANIQ has developed algorithms and FEA models to optimize multi-layer reinforcement structures for rubber products. One of the main challenges of multi-layer reinforcement structures is to efficiently activate all layers. This challenge becomes even bigger for stiff reinforcement materials like aramids. Optimization can be obtained by applying the right cord winding angles. With manual application of fabric sheet, accurate control of the winding angles is not possible. However, with the robotic winding process the cord can be accurately placed on the predetermined angles. Using the reinforcement material more efficiently you can obtain higher working pressures. TANIQ is specialized in optimization of reinforcement structures. To obtain the required working pressure products may require multiple reinforcement layers. The number of layers is determined by the total required number of cords and the optimal number of cords per layer. To obtain a good rubber-to-cord adhesion the coverage should not be too high. TANIQ has done extensive adhesion tests to find the optimal coverage per layer. The total number of cords required can be optimized by accurately winding the corda in the predetermined winding angles. Furthermore, to efficiently activate the different reinforcement layers the winding angles per layer can be adjusted.
Multi-layer reinforcement for large hoses
TANIQ has developed large hose prototypes using the robotic winding processes. These large diameter hoses of various sizes require multiple reinforcement layers to obtain the required burst pressures. Thanks to calculation of the optimal winding angles and accurate placement with the robot, up to 70% less reinforcement is used. Another advantage is continuous winding of the reinforcement over the couplings. This results in a strong connection and eliminates the manual folding step of fabric sheet and winding of metal wire to secure these sheets. For further developed and material reduction, application of different winding angles per layer is currently researched.
Multi-layer reinforcement for expansion joints
TANIQ has developed software to design optimal reinforcement structures for complex shaped products like rubber expansion joints. With this technology it becomes possible to continuously wind cords over the flanges, cylindrical parts and bellow, forming an integral reinforcement structure. Since 2012 TANIQ has demonstrated the advantages of automated production of large expansion joints and the use of optimised multi-layer structures. These expansion joints are typically designed for 64 bar burst pressure. As a result of the optimised structure and multi-layer loading, only two reinforcement layers are required. TANIQ has developed a FEM toolbox to further optimize the multi-layer reinforcement structures of expansion joints (and other products). Furthermore, TANIQ is building and testing expansion joints on daily basis to further reduce the material consumptions and increase production speeds.
Multi-layer reinforcement for high pressure hoses
TANIQ has done research and testing to explore the possibilities to improve the material efficiency for small diameter high pressure hoses by variation of the winding angels per reinforcement layer. Although it was difficult to accurately control the winding angles with the spiralling and braiding process used to make short test hoses, the results showed that higher material efficiencies can be obtained by variations of the winding angles. TANIQ has developed a basic algorithm to calculate the optimal winding angles per layer. The model is currently further optimized and validated with additional prototype testing for a large variety of hoses.
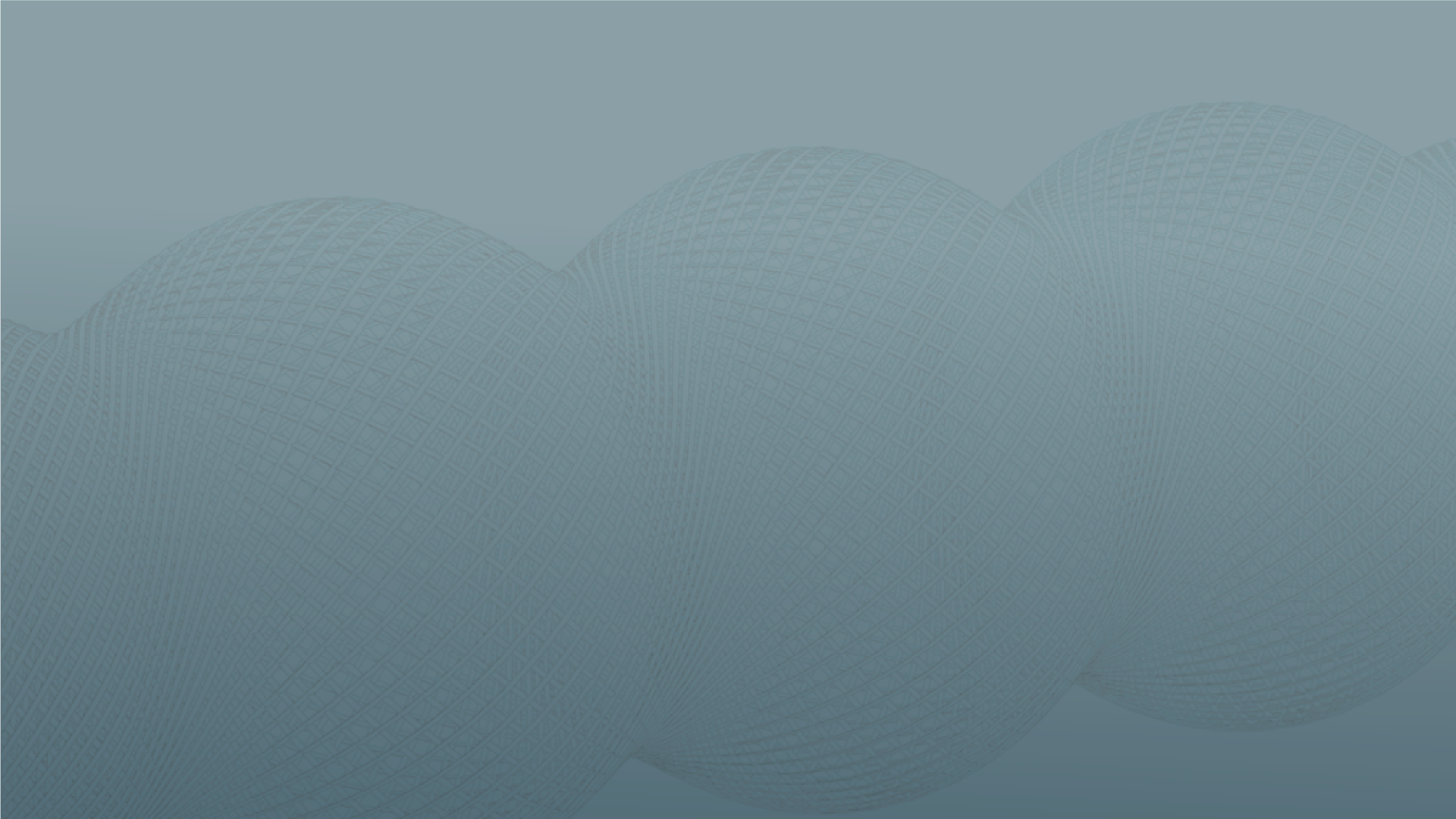