Customer Interviews - GKN Fokker
Customer Interviews
In this customer interview series, we talk with our Clients about how they experience working with TANIQ.
Interview with Ed van Breugel, Technical Authority Filament Winding from GKN Fokker Aerostructures.
In May 2023, GKN Fokker, part of GKN Aerospace, inaugurated the new Global Technology Center in Hoogeveen, the Netherlands. This cutting-edge facility serves as a dynamic environment for research and accelerated development of the latest sustainable aerospace and defense technologies. TANIQ was selected as a technology partner for developing and supplying a state-of-the-art robot-assisted filament winding machine and powerful winding software. GKN Fokker and TANIQ have closely collaborated to develop a dedicated filament winding system capable of meeting GKN Fokker’s requirements for manufacturing and developing advanced wound composite parts.
"We chose to develop this advanced system with TANIQ because of their proven expertise in developing custom robotic-assisted filament winding systems, and their in-house development of filament winding software TaniqWind.
A unique machine and a unique company!”
GKN Fokker team with TANIQ’s robotic winding machine (Image courtesy by GKN Fokker)
What is the vision behind the new Global Technology Center (GTC)?
The Netherlands GTC's primary focus will be on advancing lightweight thermoplastic composites for the next generation of aircraft while also spearheading an extensive R&D electrification program in collaboration with GKN Fokker site in Papendrecht. Additionally, the advanced robotic winding system supplied by TANIQ, being dedicated to R&D, allows for optimizing the design and manufacturing of canisters and missiles, and for developing automated winding solutions for aerospace products that are now still being manufactured by manual lay-up.
How did you know about TANIQ?
We heard about TANIQ for their expertise in rubber composites, but it is difficult to pinpoint exactly when. We later heard of TANIQ also specializing in robotics and software for filament winding and thermoplastics. What interested us from the start is that TANIQ is developing both the winding systems and the software in-house, which is very important for further development of our products and processes and struck us as a big advantage over dealing with separate suppliers for what must function as an integrated solution.
What is your project?
For the new GTC, we were looking for state-of-the-art filament winding equipment for winding composite parts for the aerospace and defense industry. Because of our specific requirements for both the hardware and software, we couldn’t get standard equipment, so we needed to develop a custom solution.
What challenges were you facing?
To achieve higher accuracy and speed on more complex shaped geometries we need more degrees of freedom, and with our current CNC winding machine, we are limited to winding 4 axes. Furthermore, the new system had to be suitable for winding both smaller parts and large/heavy parts at high speeds, which introduces a trade-off in the system design. Also, we want to use it for winding dry fibers as well as resin-preimpregnated towpregs or slitted UD tapes.
Besides the winding system, we also had specific requirements for the winding software, which we want to use next to our in-house developed software FokkerWind.
How did TANIQ’s solutions help you eliminate those challenges?
We chose to develop this advanced system with TANIQ because of their proven expertise in developing custom robotic-assisted filament winding systems, and their in-house development of filament winding software TaniqWind.
They developed a robotic-assisted filament winding system that meets all our requirements, and they got it done within the planned schedule. Furthermore, they have customized their TaniqWind Pro software for us to ensure compatibility with the programs we run on our CNC equipment, and for interaction with our internal FokkerWind software.
Their integrated solution combining the robotic system and software works smoothly and opens the door for automation of more complex parts, which we can now manufacture at high speed and high quality.
A unique machine and a unique company!
How do you see the partnership with TANIQ evolve in the future?
TANIQ engineers and I share educational backgrounds from TU Delft (Delft University of Technology), which created a mutual understanding of our engineering culture. In the future, we anticipate continued collaboration with TANIQ, exploring software improvements in TaniqWind and FokkerWind. We also look forward to seeing TANIQ's further advancements in robotics, including the incorporation of fiber placements and other innovative features.
With this R&D machine, we expect to attract more business and grow the number of wound parts to be manufactured, meaning we will need another production machine as well. A production version of the robot-assisted filament winding machine will likely also replace the existing 4-axis winding machines in time. For any developments regarding the equipment and software required to accomplish this, TANIQ will be our go-to partner.
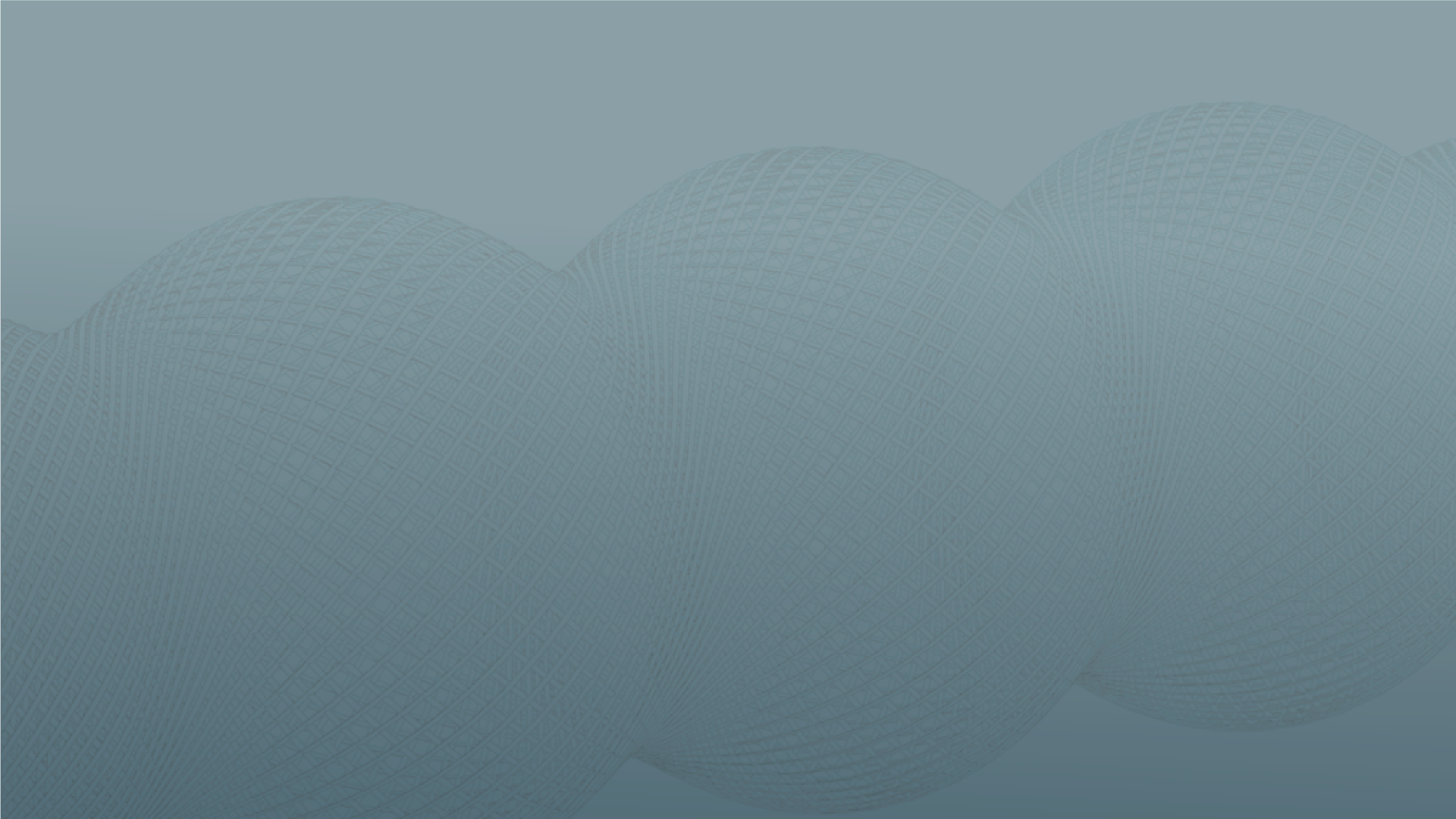